- Home
- November 2022
- USM Research to Make Cars Lighter, Cheaper and Cleaner
USM Research to Make Cars Lighter, Cheaper and Cleaner
by
Assoc. Ir. Dr. Ahmad Baharuddin bin Abdullah
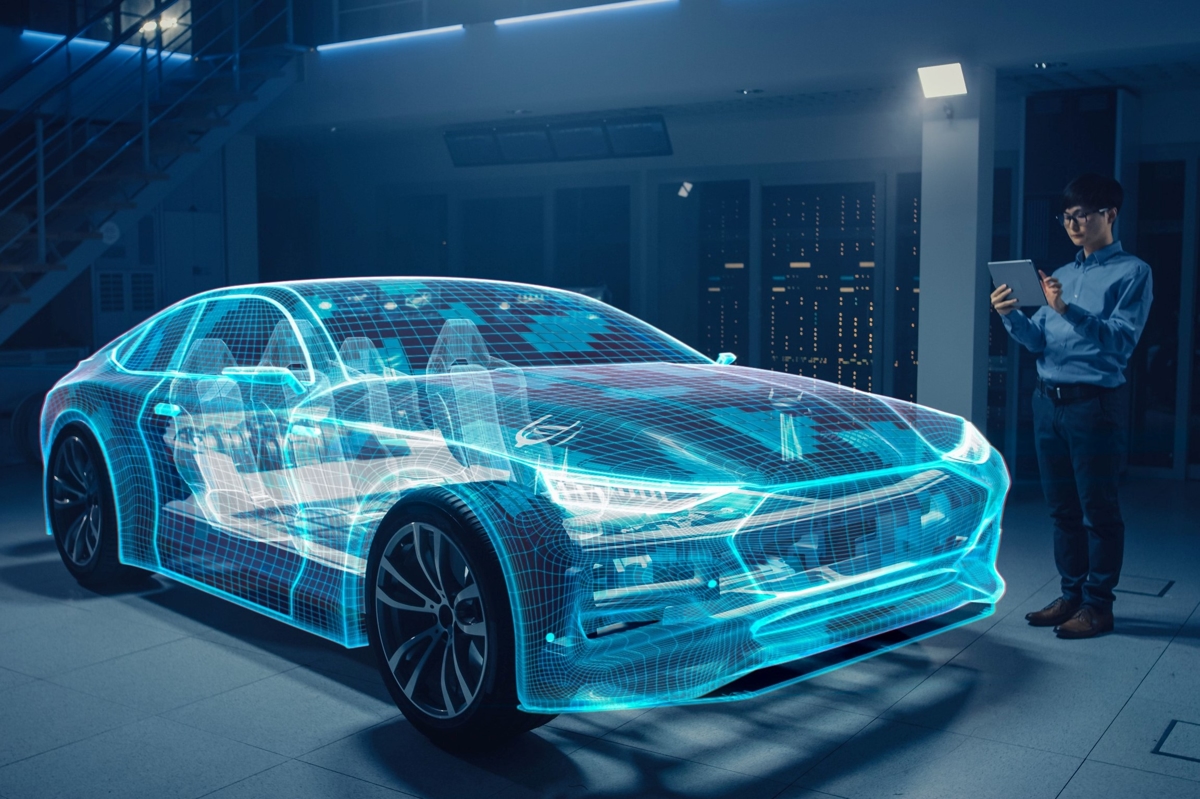
Previous Post
When Einstein Cruised into Penang
8 min read
THE CRUISE SHIP, Spectrum of the Seas, a behemoth 18-storeys high and a third of a kilometre long, sailed into Penang’s Swettenham Pier on 2 July 2022 guided by...
Next Post
The Astounding Pitcher Plants of Peninsular Malaysia
6 min read
MALAYSIA IS A wonderland for botanists, naturalists and nature lovers. Blessed with some of the oldest tropical rainforests in the world, the Peninsula itself b...
You might also like
Heralds of Dawn in the Heart of the City
4 min read
TEN MINUTES BEFORE the break of dawn, Mr. Radhi arrives at the doorstep of Masjid Melayu Lebuh Acheh to prep for the day. It is a Friday, so he is garbed in a s...
Kompang Jidor: The Rhythm of the Nusantara
6 min read
ALMOST EVERY WEEK in Kampung Parit Madirono, Pontian, Johor, a group of 12 men congregate in a balai raya or a surau. Donning baju Melayu and samping cloth, the...
When Einstein Cruised into Penang
8 min read
THE CRUISE SHIP, Spectrum of the Seas, a behemoth 18-storeys high and a third of a kilometre long, sailed into Penang’s Swettenham Pier on 2 July 2022 guided by...