- Home
- October 2021
- Green Manufacturing: One Big Step Towards a Circular Economy
Green Manufacturing: One Big Step Towards a Circular Economy
by
Dr. Nurul Bahan (School of Materials and Mineral Resources Engineering)
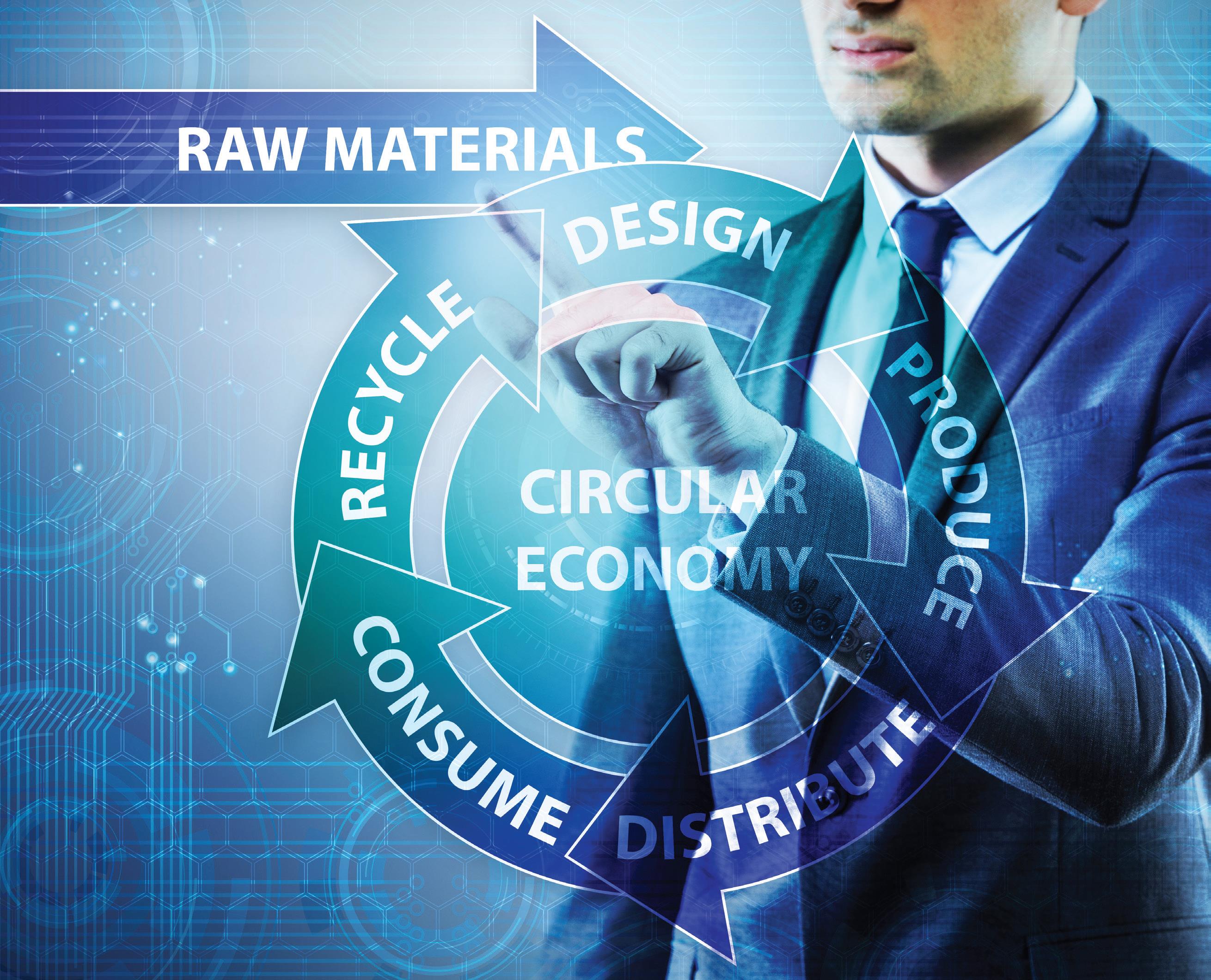
Previous Post
Chinese Tea Becoming Popular in Penang Again
4 min read
TO ENJOY A good cup of Chinese tea, much depends on how the leaves of the camellia sinensis plant is processed; through withering, oxidation, fixing or “kill gr...
Next Post
Upgrading Penang’s Shopping Possibilities
5 min read
THE SHOPPING MALLS Gurney Plaza and Gurney Paragon along the popular Gurney Drive seafront promenade form the backbone of Penang’s luxury tourism. They ca...
You might also like
No Creative Inertia for Malaysian Artists, Thank You
7 min read
WITH MORE PEOPLE getting vaccinated against Covid-19 with a view to achieving herd immunity, art spaces are opening up again, albeit still under SOPs such as we...
Introducing Culture Shot! Ethnically Diverse, Musically Intergrated
4 min read
THERE IS SOMETHING inexplicable about Penang and its local communities that is conducive to the free-flow of distinctive artistic expressions. Culture Shot came...
Chinese Tea Becoming Popular in Penang Again
4 min read
TO ENJOY A good cup of Chinese tea, much depends on how the leaves of the camellia sinensis plant is processed; through withering, oxidation, fixing or “kill gr...